The passage of the 2011 Food Safety Modernization Act enacted the most sweeping legislative changes in decades relative to food safety and shifted the focus from responding to foodborne illness outbreaks to preventing them by focusing on the prevention of contamination throughout the food supply chain.
Food safety is a top priority in manufacturing and processing facilities. Yet many overlook a critical aspect of contamination prevention: the electrical raceway system. Electrical infrastructure plays a crucial role in optimizing facility operations, balancing the requirements for production uptime, facility maintenance, and proper cleaning and sanitation with electrical safety and reliability. When poorly designed or improperly installed or maintained, electrical raceways systems can become a significant harborage point for bacteria, moisture, and debris that can directly lead to contamination risk.
According to the Robroy Food & Beverage Manufacturing Survey during pre-design, 50% of facilities replace their conduit system every 2 to 8 years due to corrosion, with contamination identified as the #1 risk concern. This highlights a major vulnerability in food production environments, where sanitation is paramount. The consequences of contamination can be severe—each year, 48 million illnesses, 128,000 hospitalizations, and 3,000 deaths occur in the U.S. due to foodborne pathogens, according to the CDC. A significant portion of food recalls are linked to foodborne illness, foreign matter, and chemical contamination, making it essential for every part of the building envolope—including raceway and utility support systems—to proactively address these risks.
Beyond the health impact, the financial burden of food recalls is staggering, with average direct costs exceeding $10 million per event. In 2023 alone, FDA food recall events increased by almost 20%, while pharmaceutical recall events surged by over 42% (Sedgwick 2023 Recall Report). These growing numbers underscore the need for facilities to implement proactive solutions that make it easier to prevent contamination at every level. Microbial growth thrives on flat, wet, and soiled surfaces, and biofilm formation accelerates corrosion, further compromising cleanability and food safety. If raceway systems are not properly sealed, bacteria can attach, grow, and spread, leading to serious contamination risks. To prevent this cycle of microbial growth and ensure long-term sanitation, food processing facilities must implement hygienically designed, corrosion-resistant electrical raceway solutions that can withstand high temperature, high pressure washdowns as an installed system. This whitepaper will explore key considerations when evaluating raceway systems and introduce a fully hygienic, NSF-certified solution from Robroy Stainless to help mitigate these risks effectively.
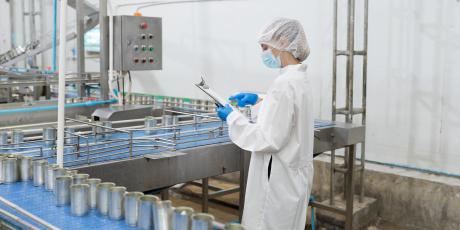
Understanding the Risks: Electrical Raceway Systems and Food Safety
Harborage Points and Contaminant Build-Up
One of the most significant risks in food processing environments is the accumulation of contaminants in electrical raceway systems. Unsealed conduit bodies, gaps, exposed threads at connection points, and crevices create the perfect environment for food particles, dust, and moisture to collect. These spaces provide an ideal breeding ground for bacteria, mold, and other harmful pathogens, which can lead to serious food safety concerns. If left unchecked, contamination in these areas can spread, affecting both product quality and compliance with strict industry regulations. To mitigate these risks, raceway systems must be designed with smooth, crevice-free surfaces that prevent buildup and allow for thorough cleaning.
Material Selection and Surface Degradation
The choice of materials used in an electrical raceway system plays a crucial role in maintaining food safety. Some metals are prone to corrosion, leading to flaking, pitting, and degradation that can introduce contaminants into food production areas. Additionally, raceways with adhesive labels, stamped markings, or rough surfaces can become harborage points for bacteria, as they are difficult to clean and can deteriorate over time. These factors not only compromise hygiene but also increase installation and maintenance costs and the risk of non-compliance with food safety standards. Facilities should prioritize corrosion-resistant materials that withstand washdowns and harsh sanitization processes without degrading over time.
System Sealing and Ingress Protection
A properly sealed electrical raceway system is essential in food processing environments. A properly sealed electrical raceway system must maintain compliance across all the components in the system in accordance with their intended use. A breach in a single component can negate the integrity of the entire system. Without proper gaskets or environmental seals, moisture and food particles can accumulate within the system, creating conditions conducive to microbial growth. High-pressure washdowns, a standard sanitation practice in food facilities, can force contaminants into hidden gaps and crevices, making it difficult to remove bacteria completely. To prevent contamination, raceway systems should feature sealed conduit bodies, optimized compression gaskets, and ingress protection ratings that ensure a barrier against dust, water, and other contaminants, thus allowing for full and complete sanitation processes.
Non-Hygienic Installation Practices
Even the best-designed electrical raceway systems can become contamination risks if they are not installed correctly. Poorly installed systems with exposed threads, misaligned components, or improper sealing create weak points where contaminants can enter and accumulate. Additionally, the lack of clear identification of hygienic vs. non-hygienic electrical components can lead to incorrect product selection and improper installation, further increasing contamination risks. To maintain compliance and ensure food safety, facilities should use raceway components specifically designed for sanitary environments, with clearly marked hygienic features that distinguish them from standard electrical infrastructure components.
By addressing these risks and implementing properly designed, corrosion-resistant, and sealed raceway systems, food processing facilities can significantly reduce contamination hazards and enhance overall food safety.
What to Look for in a Food-Safe Electrical Raceway System
When selecting an electrical raceway system for a food processing facility, it is crucial to choose components that prioritize hygiene, durability, corrosion resistance, and compliance with food and electrical safety regulations. The right system should be designed to minimize contamination risks and withstand the rigorous cleaning processes required in sanitary environments. Key features to look for include:
- Components that work together as a system of projection and performance in the environment in which they are installed.
- Seamless, non-flat, crevice-free designs that eliminate harborage points and prevent the buildup of food particles, moisture, and bacteria.
- Corrosion-resistant materials, such as 304 and 316 stainless steel, which provide superior resistance to rust, pitting, and degradation, ensuring long-term performance in harsh washdown conditions.
- IP-rated ingress protection to safeguard against moisture, debris, and high-pressure cleaning, preventing contaminants and moisture from entering the system.
- FDA-compliant materials and NSF certification, ensuring that the raceway system meets industry standards for food safety and sanitation.
- Optimized compression gaskets and sealed connections, which create a fully hygienic installation by preventing gaps where bacteria and contaminants could accumulate and moisture can enter the raceway system.
- Reduced risk of foreign matter contamination, eliminating components like paper labels, loose hardware, or exposed screws that could detach and enter the food production environment.
- 3rd Party Certification of Testing and On-going Compliance ensuring the raceway system meets industry standards for electrical safety.
By selecting a raceway system that incorporates these features, food processing facilities can significantly reduce contamination risks, improve compliance, and enhance overall plant performance, safety and sanitation.
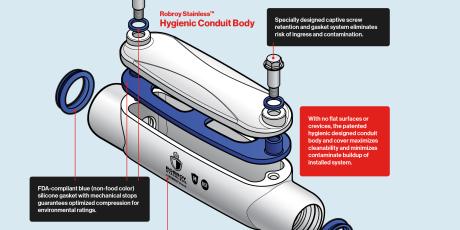
The Solution: Why Robroy Stainless Is the Best Choice for Hygienic Electrical Raceway Systems
Robroy Stainless has engineered a complete hygienic raceway solution designed to eliminate contamination risks while maintaining industry-leading performance in food processing environments. Its patented hygienic conduit body and cover feature a shape with no flat surfaces, minimizing contaminant buildup and ensuring easy cleaning. The smooth, non-porous surfaces further reduce bacterial harborage, making sanitation more effective and efficient.
To enhance environmental protection, Robroy Stainless incorporates an FDA-compliant blue silicone gasket (non-food color) designed to prevent ingress and eliminate entry points for debris and moisture. Mechanical stops ensure proper compression of the gasket, guaranteeing a secure and contamination-free installation. Additionally, the center-aligned threading and circular gasket system create a consistently sealed connection, while the IEC IP69K rating ensures the system can withstand high-pressure, high-temperature washdowns—an essential feature for food processing environments.
Robroy Stainless also reduces the risk of foreign matter contamination by utilizing Oxidative Thermo Process marking instead of adhesive labels, eliminating label degradation while ensuring long-term compliance markings without contamination risks. The captive screw retention and gasket system further safeguard against ingress and contamination while preventing small components from becoming foreign matter hazards in production areas.
For clear identification and compliance, Robroy Stainless meets major electrical listings such as UL and is NSF-certified, confirming its adherence to the strictest food safety and sanitary design standards. Additionally, the Robroy hygienic symbol helps facility managers and installers easily identify raceway components specifically designed for hygienic applications. By integrating advanced hygienic design, optimized sealing, contamination prevention, and clear identification, Robroy Stainless provides the most reliable and sanitary electrical raceway solution for food and beverage manufacturing facilities.
Conclusion: Protecting Food Safety with the Right Electrical Raceway System
Electrical raceway systems play a critical yet often overlooked role in maintaining food safety in processing environments. Without proper design and sealing, these systems can become harborage points for contaminants, posing significant risks to product integrity and regulatory compliance. Choosing a hygienically designed, fully sealed raceway system is essential to prevent contamination, reducing maintenance concerns, and ensuring long-term compliance with food safety standards. Robroy Stainless offers the most advanced hygienic raceway system, engineered for cleanability, reliability, and safety in food production facilities. By integrating industry-leading system design principles and correct materials, Robroy Stainless helps facilities meet the highest sanitary standards while maintaining operational efficiency, helping our customers maintain a safer and more reliable infrastructure.
For more information or to request a consultation, Contact Us or call (903) 843-5591.