In industrial facilities, stainless steel raceway systems are a crucial part of electrical infrastructure, especially in environments requiring corrosion resistance. Corrosion is one of the most costly and persistent challenges in industrial environments. Unchecked, it silently degrades electrical systems, infrastructure, and critical components, leading to frequent repairs, operational downtime, significant financial losses, and even personnel risks. According to a study by the Association for Materials Protection and Performance, corrosion costs industries over $2.5 trillion annually worldwide, with a substantial portion stemming from avoidable maintenance and replacements.
In sectors such as manufacturing, water treatment, chemical processing, and oil and gas, selecting the right stainless-steel system for electrical infrastructure is crucial for long-term cost savings and operational efficiency.
Understanding Corrosion Risks in Industrial Facilities
Corrosion is more than just an aesthetic issue, it is a direct threat to operational efficiency, employee safety, and regulatory compliance. While all industrial settings face some level of corrosion risk, facilities with high exposure to moisture, chemicals, and extreme temperatures are particularly vulnerable.
Corrosion in Industrial Facilities
In heavy industrial environments, corrosion can occur due to exposure to:
- Harsh chemicals and solvents used in manufacturing and processing
- High humidity and extreme temperatures that accelerate material degradation
- Salt spray and coastal exposure, which impact offshore drilling, marine, and oil and gas applications
- Abrasive conditions that cause wear and tear on electrical conduit and fittings
- Poor maintenance practices that allow small corrosion issues to grow into major failures
The result? Frequent equipment replacements, production slowdowns, and costly compliance violations. In industries where downtime can cost thousands of dollars per hour, corrosion-resistant stainless-steel solutions are essential for protecting infrastructure and ensuring reliability.
The Role of Corrosion Management in Cost Reduction
Corrosion-related failures aren’t just expensive, they’re avoidable. Data shows that the replacement cost of electrical systems that have failed due to corrosion can by 10x the original cost. Effective corrosion management strategies can help businesses significantly reduce maintenance costs, prevent downtime, and extend the lifespan of infrastructure. Key elements of corrosion management include:
1. Material Selection
When selecting a stainless-steel raceway system, choosing the right material is crucial to ensuring long-term durability and minimizing maintenance costs. Austenitic stainless steels include the common grades of 304 & 316 and provide the best corrosion resistance and best mechanical properties over a wide temperature range. 304 stainless steel is a cost-effective solution that provides excellent corrosion resistance in standard industrial environments, making it suitable for general manufacturing and indoor applications. However, for facilities exposed to harsh chemicals, saline conditions, or extreme moisture—such as chemical processing plants, wastewater treatment facilities, or coastal operations—316 stainless steel is the superior choice. Its added molybdenum content enhances resistance to chloride-induced corrosion, pitting, and oxidation, significantly extending the life of the raceway system. Selecting the appropriate stainless-steel grade for the facility’s conditions helps prevent premature failures and reduces costly replacements or repairs. Additionally, stainless steel raceway systems, such as those offered by Robroy Stainless, provide exceptional durability over alternative materials like galvanized steel or aluminum, which are more susceptible to corrode, impact damage, and environmental degradation.
Beyond material selection, it's also essential to choose a system with features specifically designed for the operational environment. For example, in industries handling oil, gas, or aggressive chemicals, selecting fittings with nitrile gaskets ensure enhanced protection against exposure to hazardous substances. These gaskets create a tight seal that safeguards electrical connections from contamination, protecting against moisture ingress, and corrosion. Furthermore, nitrile gaskets are designed to withstand extreme temperatures ranging from -40°F to 212°F (-40°C to 100°C), ensuring reliability in both high-heat and freezing conditions. By investing in a raceway system that incorporates these specialized components, industrial facilities can significantly reduce maintenance efforts while improving system integrity and safety.
2. Proper Installation
Installing stainless steel raceway systems is a straightforward process, similar to conventional conduit installations, but taking a few extra precautions can help prevent long-term issues and maximize system longevity. One critical consideration in any raceway system is the protection of threaded connections, as threads are the most vulnerable points for corrosion and contamination. Selecting a system with built-in safeguards against exposed threads can significantly enhance durability. For example, the Robroy Stainless system incorporates design protocols across the entire product offering which facilitates connection of male threads (conduit, elbows, nipples etc.,) with female threaded entries (e.g., couplings, conduit bodies, conduit hubs etc.,) in such a manner that the risk of exposed are minimized. This reduction in potential exposed threads reduces the risk of moisture intrusion, corrosion, and mechanical wear—key factors that contribute to system failures over time.
Beyond product selection, ensuring proper installation techniques is just as important. Look for a manufacturer that offers an installer certification program, which provides training on best practices for clamping, cutting, threading, bending, and assembling stainless steel conduit systems. These programs help installers understand the nuances of working with stainless steel, including how to maintain the material’s integrity, prevent contamination, and apply proper torque settings for secure connections. By investing in both high-quality materials and trained installers, facilities can achieve a robust, long-lasting raceway system that minimizes maintenance costs and maximizes reliability in demanding industrial environments.
3. Preventative Maintenance
Proper maintenance of stainless-steel raceway systems will ensure long-term reliability and prevent costly failures. One of the most common issues arises from improper cleaning methods or the use of incompatible chemicals, which can degrade the material and compromise system integrity. Educating maintenance staff on correct care procedures—such as using non-abrasive cleaners, avoiding chloride-based solutions, and following proper rinsing techniques—helps preserve the corrosion-resistant properties of stainless steel. Additionally, keeping detailed installation and maintenance records ensures continuity of operations, minimizes errors when personnel change, and helps teams track inspections and preventive maintenance schedules effectively.
Regular maintenance checks should focus on visual inspections for signs of corrosion, loose covers, or dust or liquid contamination, torque verification on connections to ensure mechanical integrity, and cleaning schedules that remove debris buildup in hygienic environments. Facilities should also look for built-in design features that help mitigate potential issues before they arise. Additionally, the oxidative thermo marking process provides dark, permanent product information without degradation to the product surface. By combining proactive maintenance practices with intelligently designed system features, facilities can significantly reduce downtime, extend the lifespan of their raceway systems, and maintain compliance with industry regulations.
4. Compliance with Industry Standards
When selecting a stainless-steel raceway system for an industrial environment, ensuring compliance with industry standards is critical to guaranteeing safety, performance, and longevity. A high-quality system should be certified to independent third party and industry standards. Third party certification provides evidence that the conduit and fittings are tested and verified for on-going compliance for electrical safety and applicable environmental ratings both of which are NEC (National Electrical Code) requirements. A rating of UL Type 4X signifies protection against corrosion, water ingress, and environmental exposure in accordance with UL standard 50E, making it ideal for washdown areas, food processing plants, and other harsh environments. Depending on the application, facilities may also look for compliance with NSF standards. The NSF mark serves as evidence that products are independently certified to meet or exceed requisite NSF standards for hygienic environments. Ingress Protection Ratings (IP) show evidence of approval and compliance in accordance with IEC (International Electrotechnical Commission) standards for global regulatory adherence.
Beyond compliance, ensuring that safety and certification markings remain legible in harsh environments is crucial for long-term performance and regulatory adherence. One of the standout features of the Robroy Stainless system is its Oxidative Thermo Process (OTP) marking, which creates a permanent label that will not fade, peel, or deteriorate—even in the most challenging environments. This marking method is particularly beneficial in facilities where exposure to chemicals, moisture, extreme temperatures, and frequent washdowns can cause traditional labels to degrade. This ensures that critical compliance information—such as listing or ratings—remains intact, preventing confusion during inspections, maintenance, and audits. It also enhances inspection, allowing facilities to quickly verify that their raceway system meets the required standards for their environment. By choosing a system with long-lasting, non-degradable identification, industrial facilities can avoid costly compliance issues, streamline maintenance efforts, and ensure that essential safety information is always available, regardless of operational conditions.
5. Long-Term Cost Savings
Look for systems with built-in design features that can make a significant difference in both the ease of installation and long-term maintenance. A well-designed system, such as Robroy Stainless, is engineered for durability and efficiency, allowing industrial facilities to streamline maintenance, minimize unexpected downtime, and improve overall operational efficiency. These thoughtful design elements reduce installation errors, extend the service life of the system, and ultimately lower overall maintenance expenses, making it a smart investment for long-term performance.
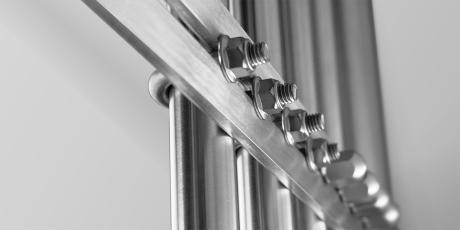
Why Robroy Stainless is the Best Choice for Stainless Steel Raceways in Industrial Environments
When it comes to industrial stainless steel raceway systems, Robroy Stainless stands out as the superior choice for facilities that demand durability, reliability, and long-term performance. Designed with precision engineering and industry-leading features, the Robroy Stainless Industrial Line ensures optimal protection against harsh environmental conditions while simplifying installation and maintenance. Key features include:
- Options in 304 and 316 Stainless Steel – Available in both 304 and 316 stainless steel, providing a full line of conduit, fittings, and accessories to meet the specific needs of different industrial environments.
- Electropolished Finish – Enhances corrosion resistance, improves cleanability, and provides a sleek, aesthetically pleasing appearance.
- Center-Aligned Threading – Ensures environmental safety ratings are met, guaranteeing a properly sealed and compliant installation.
- Stamped Cover with Nitrile Gasket – Provides superior protection against dirt, rain, sleet, snow, windblown dust, and hose-directed water, ensuring long-term sealing integrity and resistance to petroleum-based oils and harsh chemicals.
- Oxidative Thermo Process (OTP) Marking – Creates a permanent label that will not fade, peel, or degrade, even in outdoor or corrosive environments, ensuring lasting identification for compliance and traceability.
- Complimentary Installer Certification Training – Ensures installers are properly trained on best practices for cutting, threading, bending, clamping, and assembling stainless steel raceway systems, reducing installation errors and maximizing system longevity.
With these innovative features, Robroy Stainless delivers a raceway system that not only meets industry standards but exceeds expectations for longevity, performance, and ease of maintenance. By choosing Robroy Stainless, industrial facilities can reduce downtime, lower long-term maintenance costs, and ensure the integrity of their electrical infrastructure for years to come.
Reduce Maintenance Costs with Robroy Stainless
Businesses across industrial sectors are recognizing that corrosion resistance is a key factor in lowering long-term total ownership costs. Robroy Stainless offers the ideal solution for corrosion protection, regulatory compliance, and cost-effective performance.
Ready to eliminate corrosion-related maintenance costs and extend the lifespan of your infrastructure?
Contact us today and discover the difference stainless steel can make in your facility.